Order pickers have a strenuous and time-consuming job while executing their work in a warehouse. In an order fulfilment process, order picking is one of the most vital components to be considered. According to a validated insight, more than half of warehouse operating costs are attributed to order picking. In order to choose the best order picking methods, you need to understand the nature of your business.
An extensive and thorough picking and packing process in the warehouse contributes directly toward fast and on-point order fulfilment that is invariably brought in customer satisfaction. Regarding this, the particular method that you opt for your order picking operations becomes vital.
What is Order Picking?
When it comes to the question of what is order picking, it becomes extremely necessary to understand the concept from a larger perspective. As phonetically it suggests, the literal meaning of the term order picking accurately fits the same, with it being defined as the procedure that involves retrieving products from the warehouse in order to fulfil a customer’s orders.
The typical trait of order picking is a labour-intensive activity and requires elements of speed and accuracy. Productivity levels also are vital here, since the amount of time which is taken to procure an order influences the delivery time.
Most of the time of the order pickers is spent searching for and pulling respective items in a warehouse. Fortunately, there are some the picking methods which help in cutting down on such travel time thereby enhancing order fulfilment of your business each day.
The Importance
Going forward, order picking at times becomes so essential a customer’s positive or negative experience depends heavily on the results brought in by the picking process. Only when you execute absolute efficiency in order accuracy and timely order fulfilment, it is then you unlock to retain a happy customer thereby providing him or her with an overall satisfying shopping experience.
Other than customer satisfaction being a determining factor here, having warehouse picking best practices also further helps you in gaining significant labour cost savings too.
Practising efficient picking furthermore reduces operating time and elevates accuracy levels of the picking process. Having a good inventory control system in place undoubtedly goes a long way in improvising picking accuracy.
Types of Order Picking
Here are handpicked six types of order picking methods that help heavily in supporting an efficient and profitable operation.
Single order picking
One of the most basic and preliminary order picking methods is single order packing. Although pretty much considered to be time-consuming yet due to its various other beneficial aspects it fixates its position in this list. In a single 9rdrpciking system, a picker works in singular order one at a time.
Each item is sorted and found out in the warehouse one by one in order to complete the respective order. This means, that most often pickers travel along the same route on a repeated frequency throughout their shift.
Mostly, single order picking is best suggested for smaller warehouses which operate on minimum order numbers and handles smaller volumes of order deliveries. According to experts, single order picking benefits in maintaining accuracy, since the pickers are asked to work on just single order one at a time.
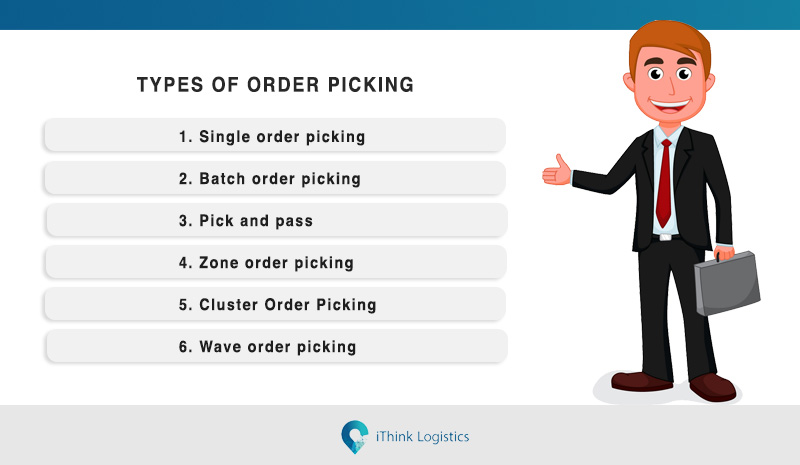
Batch order picking
Another name with which batch order picking is known is multi-order picking. This procedure permits pickers to execute the work on multiple orders in a single frame of time i.e. at a time, one SKU.
Companies that deal with multiple orders which have the same SKUs (items) or orders that have only a few SKUs are recommended for batch order picking. Along with cutting down on travel time, and managing various orders around a single time, a picker needs to deliver an item via each delivery cycle.
Pick and pass
The pick and pass method denotes a system where the warehouse is divided into multiple zones with pickers or workers assigned in each of them. The picking system involves associates retrieving SKUs for various orders from within their totes, zone, bins or containers at a time. It is then passed on to the next zone for the following step of actions yet to be taken. The terms pick and pass are more often used interchangeably with zone picking. However, in this case, zone picking can be executed without the bins or containers being passed from one zone to another.
Zone order picking
Having a very close workability model to that of the pick and pass method, zone order picking is combinational with other methods. In a zone order picking system, the warehouse is split into various zones. The work is equally divided among the pickers who are assigned their respective zones from where must pull items.
The order container is passed to the following zone, which requires having products from multiple zones. The respective zone’s picker carries on continuing picking items for the next bulk orders. Until the order is completed and fulfilled, the process goes on.
Zone order picking is highly efficient and recommended for warehouses which deal with high volume inventories and faces the challenge of picker congestion in different areas.
Cluster Order Picking
Allowing pickers to execute their work on various orders within the same time, the cluster order picking method comes into action. Instead of focusing on some kind of SKUs (items) for several orders, pickers get to pick multiple items for different orders.
Other ways like vertical lift modules or carousels can be also used to accomplish this, however, the most basic and common method is where a picker loads the cart with multiple containers. To help in the reduction of errors, pickers take use of a collaborative mobile robot or an order picking cart.
The cluster order picking method reduces travelling time but not as much as the batch order picking system. In this method, the picker travels to a respective zone or area one at a time for each cluster they are assigned to work on.
Wave order picking
In a wave order picking system, pickers operate their work within their respective assigned zones. With regards to cutting down on time, all areas are picked along the same time, opposing operating from one zone and then passed onto the next. Further to this, the products or items are then segregated and consolidated into their individual shipments.
In a typical wave order picking there is an additional requirement of more workers for the consolidation and sorting process making it a time-consuming process; however, as compared to the rest other wave order is actually much quicker and exercises the ability to move onto the order to various zone rather than waiting for each zone to execute their part of the job.
Wave order picking is best considered and recommended for companies that have a higher number of picks with respect to each order.
Which order picking method should you choose?
Now that you have gone through all the handpicked order picking best practices, you must be wondering which stands out for you in the most profitable way. When it comes to choosing an order picking method, batch picking is the best option to choose from. This is because batch picking help in quicker order fulfilment. The basic factor to keep in mind is that it heavily depends on the type of company you have and the volume of orders you deal with each day.
Other than that, it also depends on big is your warehouse and the amount of inventory you have in stock. Based on questions like, how many orders you manage and receive each day, how many products are there in respective orders, or how many pickers you have, you need to conclude and decide exactly which order picking method works the best for you.
Conclusion
To ensure the highest levels of success and efficiency, select a method from stands outright for your company, and can opt for combining them with automated technologies.